Fill in the form to be notified of product releases
The toothbrush
It’s the most widely used bathroom item in France and the world! 200 million toothbrushes are sold every year in France, but only 5% are produced domestically.
Toothbrushes made of wood, virgin plastic, bio-plastic, recycled plastic; with or without interchangeable heads; electric or manual… There are many different kinds of toothbrushes today, but did you know that the vast majority are imported from Asia?
At Sementis, we’ve chosen to invest in the French toothbrush, through a production tool: a stacking machine. A machine for what? Stacking is the process of attaching filaments to a base, which can come in a variety of shapes and materials.
Want to know more?
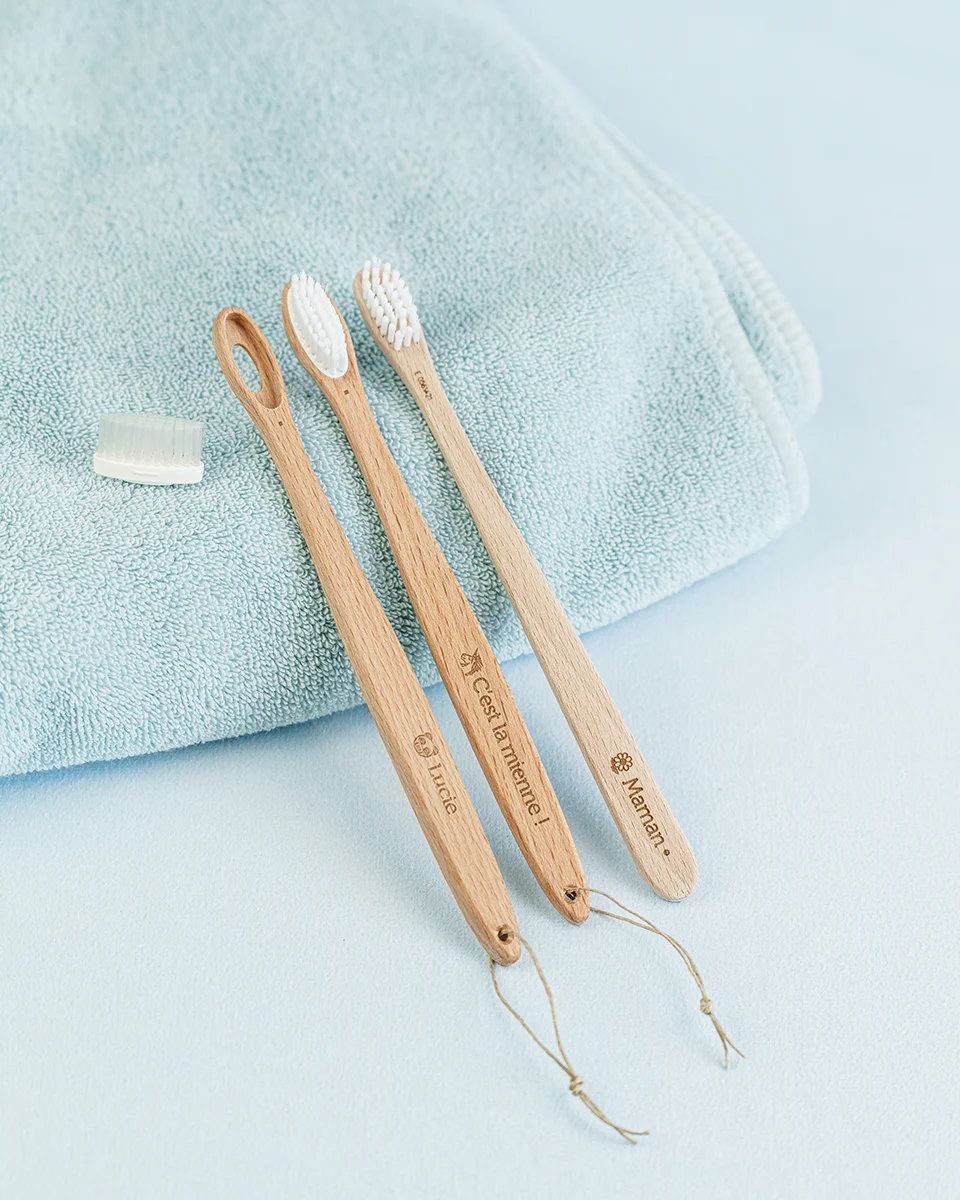
What’s a toothbrush?
A HANDLE
15g is the average weight of a toothbrush today! And the handle accounts for almost 90% of the product’s weight. So what could be more logical than thinking in terms of eco-responsible materials or limiting the waste associated with this component?
For us, this is a key issue, and our team is working hard to offer you solutions that are adapted, consistent with our approach and local.
Thanks to our 5 years’ experience with J’aime mes dents ! and with our customers, we’ve been able to experiment with different solutions: bamboo toothbrushes, French wooden toothbrushes with and without interchangeable heads, bio-plastic toothbrushes with interchangeable heads… and each has its advantages and disadvantages!
Today, we’ve made a strong choice regarding the provenance of our raw materials: they’ll be French (or European if necessary)!
The wood used for our handles is French (cocorico), sourced from eco-managed forests in eastern France. To optimize the durability of our products, handles are oiled with vegetable oil or varnished without volatile elements.
The plastic (yes, we did say plastic) used for our interchangeable head bases or for the handles we work on is biosourced or recycled.
FILAMENTS
Or bristles, to put it mildly! This is the main component of the toothbrush, in terms of use (yes, in terms of weight, it’s the handle that takes the prize, as we explained above).
We were talking about European raw materials, and indeed this is the case for this material. Germany has preserved the know-how that we (unfortunately) no longer have in France.
Our filaments are 70% vegetable-based and we’re very proud of that. If we work them in the right way, we can offer you a complete range of toothbrushes with different hardnesses (extra-soft, soft, medium…), as well as unique products (thanks to the colors).
How is a toothbrush made?
As you can see, very few of us have the know-how to manufacture toothbrushes in France. And we’re even less likely to make our manufacturing tools available to brands other than our own. It’s important to explain how we go from a handle/base to an interchangeable toothbrush/head.
01.
DRILLING
This step is essential for wooden toothbrushes, and only wooden ones. Wooden handles arrive undrilled from our French partner and are drilled directly on our production line. This guarantees precision and quality.
The plastic is already perforated. This step is carried out directly when the part is injected.
02.
STACKING
This is the key stage in toothbrush manufacture. It involves attaching filaments to a handle or base of any material. Anchors and filaments are then inserted to form a toothbrush.
03.
CUTTING
This involves cutting the filaments to the height decided during production. Along with various other parameters, this length will influence the hardness of the toothbrush.
04.
ROUNDING
This last step is not visible to the naked eye, but it helps to avoid damaging the gums of users by rounding off the ends of the filaments.